Two years ago, we introduced MotoCAP (Motorcycle Clothing Assessment Program), an Australia- and New Zealand-based resource evaluating the technical aspects and materials of protective motorcycle gear, including jackets, pants, gloves, and helmets. We’ve also reported on safety performance standards for helmets, faceshields, gloves, and general motorcycle riding apparel.
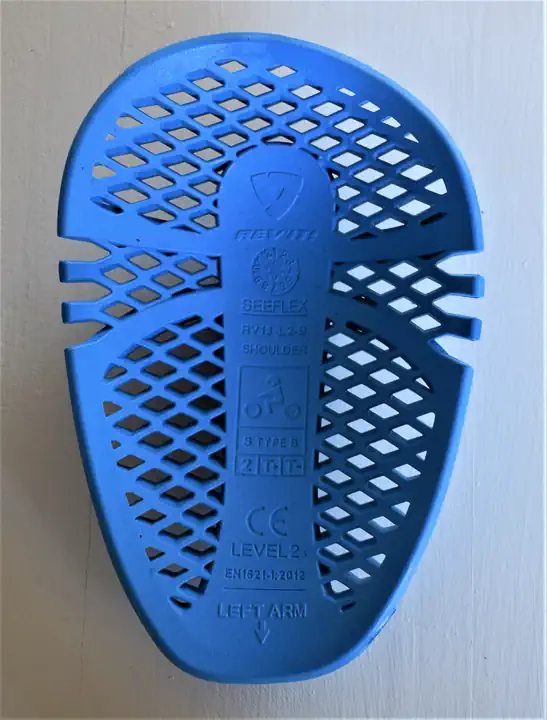
Now, MotoCAP has expanded its testing to include impact protectors in motorcycle jackets and pants, further ensuring rider safety. These garments, including their impact protectors, are evaluated for impact protection, abrasion resistance, breathability, seam burst resistance, and water resistance (when waterproofing claims are made).
Here are the MotoCAP testing protocols:
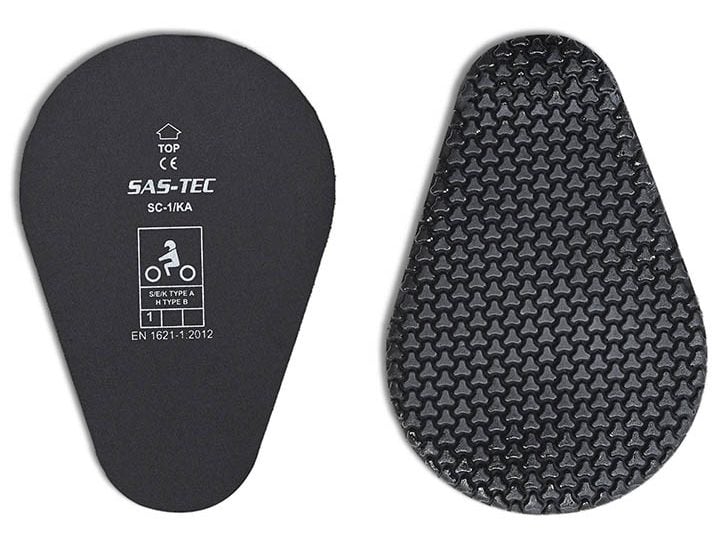
- Abrasion resistance. This test assesses how long the garment will protect the wearer from abrasion when contacting a paved road surface. A sample is wrapped around a solid metal block on an arm, dropped onto an abrasive belt moving at a fixed speed, and a timer started. When a hole forms in the material, a thin wire behind the material is broken, automatically stopping the timer. The longer the time before the material fails, the higher its abrasion resistance.
- Thermal comfort. Thermal comfort is assessed by determining the breathability of the garment. This is important because a person can be physically affected by hyperthermia—the elevation of the body’s core temperature. The body’s defense mechanism against this condition is perspiration. As sweat evaporates, it provides a cooling effect. If the garment does not allow this to happen, overheating can result.
The test provides a breathability score based on the relative vapor permeability index, which measures how easily sweat vapor escapes through the fabric. The higher the score, the better the breathability is, which improves thermal comfort.
While MotoCAP assesses joint impact protectors, it does not rate back protectors. A sample is placed in a temperature-controlled cabinet over a hot plate, where heated water is injected onto the plate’s surface to simulate sweat on a rider’s skin. This is the “wet” portion of the test.
As the simulated sweat passes through the fabric to escape to the environment, more sweat will be created to maintain the hot plate temperature. The sweat that travels through the fabric is measured by monitoring the energy required to heat the hot plate.
The thermal resistance component of the test consists of using the same cabinet as the wet test. However, the heat source is kept dry. Performance is measured by monitoring the energy required to maintain the temperature of the underlying simulated skin membrane.
- Water resistance. Water is sprayed onto a test dummy seated on a motorcycle and exposed for 20 minutes to water sprayed at the motorcycle’s headlight under high pressure from two meters away. The test measures the amount of water that enters the gear and wets the underclothing.
The test dummy is dressed in long cotton undergarments, with cotton gloves and socks under riding gear. Water that reaches the cotton undergarments through the riding gear wets the cotton underlayer. The undergarment is weighed at the end of the test period to determine water resistance. - Burst test. A burst test is performed on a motorcycle jacket sample to record its seams’ strength. The sample, which includes a portion with a seam, is inflated under pressure until the stitching on the seam bursts or the maximum test pressure is reached. The maximum pressure achieved determines the burst resistance score.
MotoCAP indicates its motorcycle gear safety ratings are based on independent scientific tests—not reliant on data reported by the manufacturer. For more details on the test process and ratings, go to the MotoCAP website.